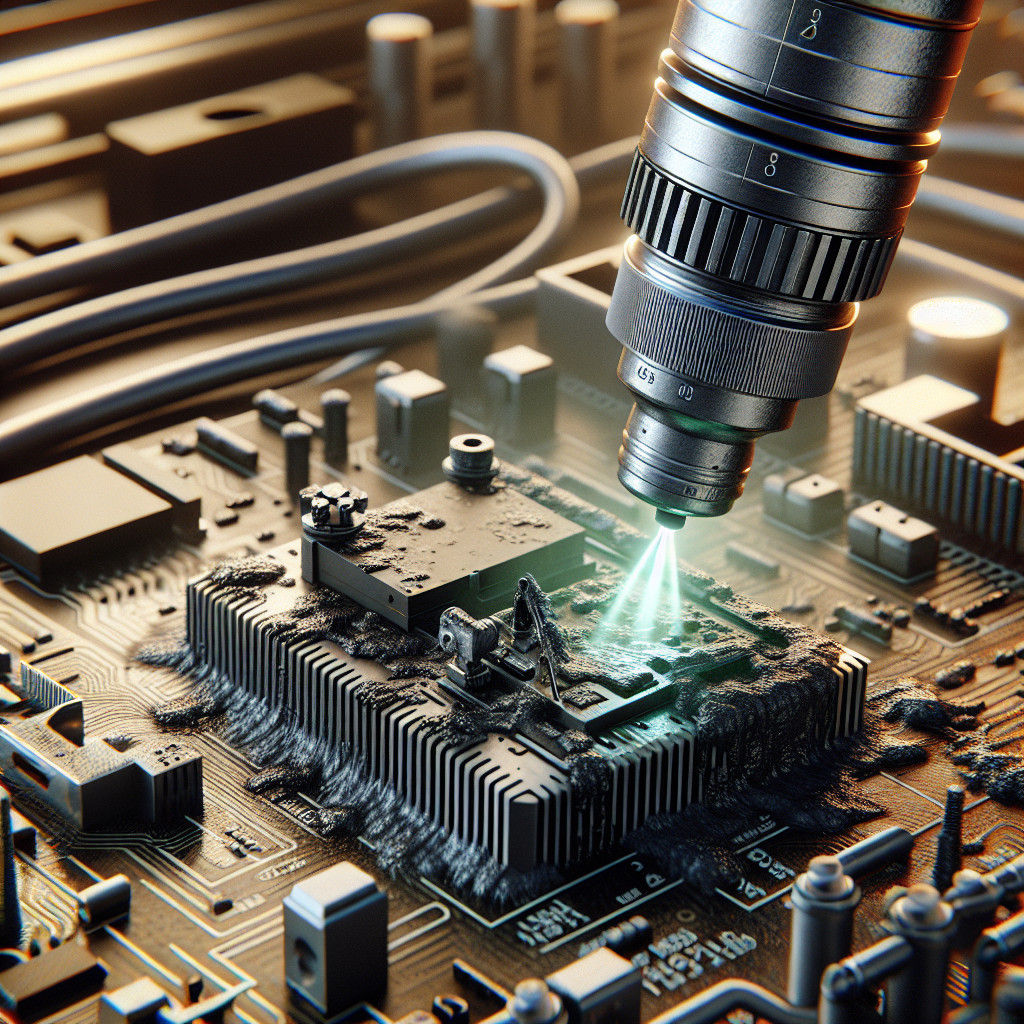
- History of laser cleaning in electronics industry
- Types of contaminants removed by laser cleaning
- How does laser cleaning work on circuit boards?
- Cost-effectiveness of laser cleaning for circuit boards
- Laser cleaning for removing solder flux residues from circuit boards
- Laser cleaning for removing thermal paste and grease from circuit boards
- Laser cleaning for removing contaminants from multi-layer circuit boards
- Types of contaminants removed by laser cleaning
History of laser cleaning in electronics industry
Early developments:
- The concept of using lasers for cleaning purposes was first explored in the 1970s, with researchers experimenting with various laser types and wavelengths to determine their effectiveness in removing contaminants from surfaces.
- By the 1980s, laser cleaning technology had advanced significantly, with the development of more powerful and precise lasers that could target specific contaminants without damaging the underlying material.
Advancements in the 21st century:
- In the early 2000s, laser cleaning technology began to gain widespread adoption in the electronics industry, as manufacturers recognized the benefits of using lasers for precision cleaning of components.
- Today, laser cleaning systems are used in a wide range of electronic manufacturing processes, including PCB assembly, semiconductor fabrication, and precision optics manufacturing.
Future prospects:
As laser cleaning technology continues to evolve, researchers are exploring new applications for this technology in the electronics industry, such as cleaning of 3D printed components and advanced materials.
Keywords: laser cleaning, electronics industry, contaminants, precision, technology
Long-tail phrases: history of laser cleaning, advancements in laser cleaning technology, future prospects of laser cleaning in electronics industry
#laser #cleaning #electronics #industry #contaminants #precision #technology
history of laser cleaning, advancements in laser cleaning technology, future prospects of laser cleaning in electronics industry
Types of contaminants removed by laser cleaning
🔹 Paint: Paint can be easily stripped away using laser cleaning, making it a popular choice for removing old paint from surfaces.
🔹 Grease and oil: Laser cleaning can also remove grease and oil from surfaces, making it ideal for cleaning machinery and equipment.
🔹 Oxidation: Laser cleaning can remove oxidation from metal surfaces, improving their appearance and longevity.
🔹 Dirt and grime: Laser cleaning is effective at removing dirt and grime from surfaces, leaving them clean and pristine.
In addition to these common contaminants, laser cleaning can also remove other types of unwanted materials, such as:
🔸 Adhesives: Laser cleaning can remove adhesives from surfaces without damaging the underlying material.
🔸 Coatings: Laser cleaning can strip away coatings from surfaces, allowing for easy reapplication of new coatings.
🔸 Corrosion: Laser cleaning can remove corrosion from metal surfaces, preventing further damage and extending the lifespan of the material.
Overall, laser cleaning is a versatile and efficient method of removing a wide range of contaminants from surfaces. Whether you need to remove rust, paint, grease, or any other unwanted material, laser cleaning can provide a fast and effective solution.
#laser #cleaning #contaminants #removal #rust #paint #grease #oil #oxidation #dirt #grime
Keywords: laser cleaning, contaminants, removal, rust, paint, grease, oil, oxidation, dirt, grime
Long-tail phrases: laser cleaning for rust removal, effective paint stripping with laser cleaning, benefits of laser cleaning for grease and oil removal.
How does laser cleaning work on circuit boards?
- Preparation: Before the cleaning process begins, the circuit board is inspected to identify the type and extent of contamination. This information helps determine the appropriate laser settings for optimal results.
- Laser beam application: A high-powered laser beam is directed onto the contaminated areas of the circuit board. The energy from the laser heats up and vaporizes the contaminants, which are then removed by a vacuum system.
- Controlled process: Laser cleaning is a precise and controlled process that can be adjusted to target specific contaminants while avoiding damage to the underlying components. This level of precision makes it ideal for cleaning circuit boards with intricate designs.
- Post-cleaning inspection: Once the cleaning process is complete, the circuit board is inspected to ensure that all contaminants have been successfully removed. Any remaining residue can be addressed with additional laser cleaning or alternative methods.
Overall, laser cleaning offers a non-contact and environmentally friendly solution for removing contaminants from circuit boards. It is a versatile technique that can be used for a wide range of applications in the electronics industry.
Keywords: laser cleaning, circuit boards, contaminants, precision, non-contact, environmentally friendly
Long-tail phrases: laser cleaning process on circuit boards, removing contaminants with laser technology, precision cleaning for delicate components
#laser #cleaning #circuitboards #contaminants #precision #noncontact #environmentallyfriendly, laser cleaning, circuit boards, contaminants, precision, non-contact, environmentally friendly, laser cleaning process on circuit boards, removing contaminants with laser technology, precision cleaning for delicate components
Cost-effectiveness of laser cleaning for circuit boards
The cost-effectiveness of laser cleaning for circuit boards lies in its efficiency and long-term benefits. While the initial investment in laser cleaning equipment may be higher than traditional cleaning methods, the savings in labor costs, reduced downtime, and improved product quality can outweigh the upfront costs in the long run.
Laser cleaning is a non-contact process, which means that there is no risk of damage to the delicate components of the circuit board. This reduces the need for costly repairs or replacements, saving companies money in the long term.
Furthermore, laser cleaning is a more environmentally friendly option compared to traditional cleaning methods. Since no chemicals or solvents are used in the process, there is no risk of harmful substances being released into the environment.
In conclusion, laser cleaning for circuit boards is a cost-effective solution that offers numerous benefits in terms of efficiency, precision, and environmental sustainability. Investing in laser cleaning technology can help companies improve their bottom line while also reducing their impact on the environment.
- Efficiency
- Precision
- Longevity
- Environmental sustainability
- Cost-effectiveness
- Improved product quality
- Reduced downtime
- Labor cost savings
- Non-contact process
- Reduced risk of damage
#laser cleaning, circuit boards, cost-effectiveness, efficiency, precision, longevity, environmental sustainability, improved product quality, reduced downtime, labor cost savings, non-contact process, reduced risk of damage
Laser cleaning for removing solder flux residues from circuit boards
One of the key advantages of laser cleaning is its precision. The laser beam can be focused to a very small spot size, allowing for targeted cleaning of specific areas on the circuit board. This level of precision is especially important in the electronics industry, where even small amounts of residue can cause significant problems.
Laser cleaning is also environmentally friendly, as it does not require the use of chemicals that can be harmful to the environment. Additionally, the process produces minimal waste, as the residues are vaporized and removed from the surface of the circuit board.
Overall, laser cleaning is a highly effective and efficient method for removing solder flux residues from circuit boards. It offers precision, speed, and environmental benefits that make it an ideal choice for electronics manufacturers looking to improve the quality and reliability of their products.
Keywords:
- Laser cleaning
- Solder flux residues
- Circuit boards
- Electronics manufacturing
- Precision cleaning
Long-tail phrases:
- Non-contact method for removing solder flux residues
- Environmentally friendly cleaning solution for electronics industry
- High precision laser cleaning for circuit board maintenance
#laser #cleaning #solderflux #residues #circuitboards #electronics #manufacturing #precisioncleaning #environmentallyfriendly #longtailphrases #noncontactmethod #highprecision #cleaningsolution
Laser cleaning for removing thermal paste and grease from circuit boards
One of the main advantages of laser cleaning is its precision. The laser beam can be focused to a very small spot size, allowing for targeted cleaning of specific areas on the circuit board. This is particularly useful when dealing with intricate designs or densely packed components where traditional cleaning methods may not be able to reach.
Another benefit of laser cleaning is its efficiency. The process is quick and effective, removing contaminants in a matter of seconds without the need for harsh chemicals or abrasive materials. This not only saves time but also reduces the risk of damage to the circuit board and its components.
Furthermore, laser cleaning is a environmentally friendly solution as it does not produce any waste or harmful byproducts. Unlike traditional cleaning methods that may involve the use of chemicals or solvents, laser cleaning is a clean and sustainable process that is safe for both the operator and the environment.
In conclusion, laser cleaning is a highly effective and efficient solution for removing thermal paste and grease from circuit boards. Its precision, speed, and environmental friendliness make it an ideal choice for cleaning delicate electronic components without causing damage. With the increasing demand for clean and reliable electronics, laser cleaning is set to become a standard practice in the industry.
- precision
- efficiency
- environmentally friendly
- non-contact
- quick
- removing thermal paste and grease from circuit boards
- cleaning delicate electronic components
- targeted cleaning of specific areas
- high-powered laser beam
- clean and sustainable process
#laser #cleaning #thermalpaste #grease #circuitboards #electronics #precision #efficiency #environmentallyfriendly
Laser cleaning for removing contaminants from multi-layer circuit boards
How laser cleaning works
Laser cleaning utilizes a high-energy laser beam to remove contaminants from the surface of a multi-layer circuit board. The laser beam is directed at the contaminated area, where it vaporizes the contaminants without damaging the underlying material. The process is highly precise, allowing for targeted cleaning of specific areas on the circuit board. Laser cleaning is also non-contact, meaning that there is no physical contact between the laser beam and the circuit board, reducing the risk of damage to the components.
Benefits of laser cleaning
There are several benefits to using laser cleaning for removing contaminants from multi-layer circuit boards. Some of the key advantages include:
Benefits | Description |
---|---|
Precision | Laser cleaning allows for precise removal of contaminants without damaging the underlying material. |
Efficiency | Laser cleaning is a fast and efficient process, reducing the time required for cleaning multi-layer circuit boards. |
Non-contact | There is no physical contact between the laser beam and the circuit board, reducing the risk of damage to the components. |
Environmentally friendly | Laser cleaning does not require the use of chemicals or solvents, making it an environmentally friendly cleaning solution. |
Conclusion
Laser cleaning is a highly effective and efficient method for removing contaminants from multi-layer circuit boards. Its precision, efficiency, and environmentally friendly nature make it an ideal solution for cleaning delicate electronic components. By utilizing laser cleaning technology, manufacturers can ensure the reliability and performance of their multi-layer circuit boards.
#laser #cleaning #multi-layer #circuit #boards #contaminants #precision #efficiency #non-contact #environmentally friendly
słowa kluczowe: laser cleaning, multi-layer circuit boards, contaminants, precision, efficiency, non-contact, environmentally friendly
frazy kluczowe: laser cleaning for multi-layer circuit boards, precision cleaning of contaminants, efficient removal of contaminants from circuit boards, environmentally friendly cleaning solution.
Types of contaminants removed by laser cleaning
Contaminant | Description |
---|---|
Rust | Oxidation of iron or steel surfaces |
Paint | Coatings applied to surfaces for protection or decoration |
Grease | Oily substances that can accumulate on surfaces |
Corrosion | Deterioration of metal surfaces due to chemical reactions |
Scale | Mineral deposits that can build up on surfaces |
These are just a few examples of the types of contaminants that can be effectively removed by laser cleaning. The versatility and precision of laser cleaning make it an ideal solution for a wide range of cleaning applications.
Hashtags: #laser #cleaning #contaminants #removal
Keywords: laser cleaning, contaminants, removal, surfaces
Long-tail phrases: types of contaminants removed by laser cleaning, laser cleaning applications, laser cleaning benefits
- Laser cleaning for removing contaminants from leather surfaces - 4 August 2024
- Laser cleaning for removing contaminants from circuit boards - 24 April 2024