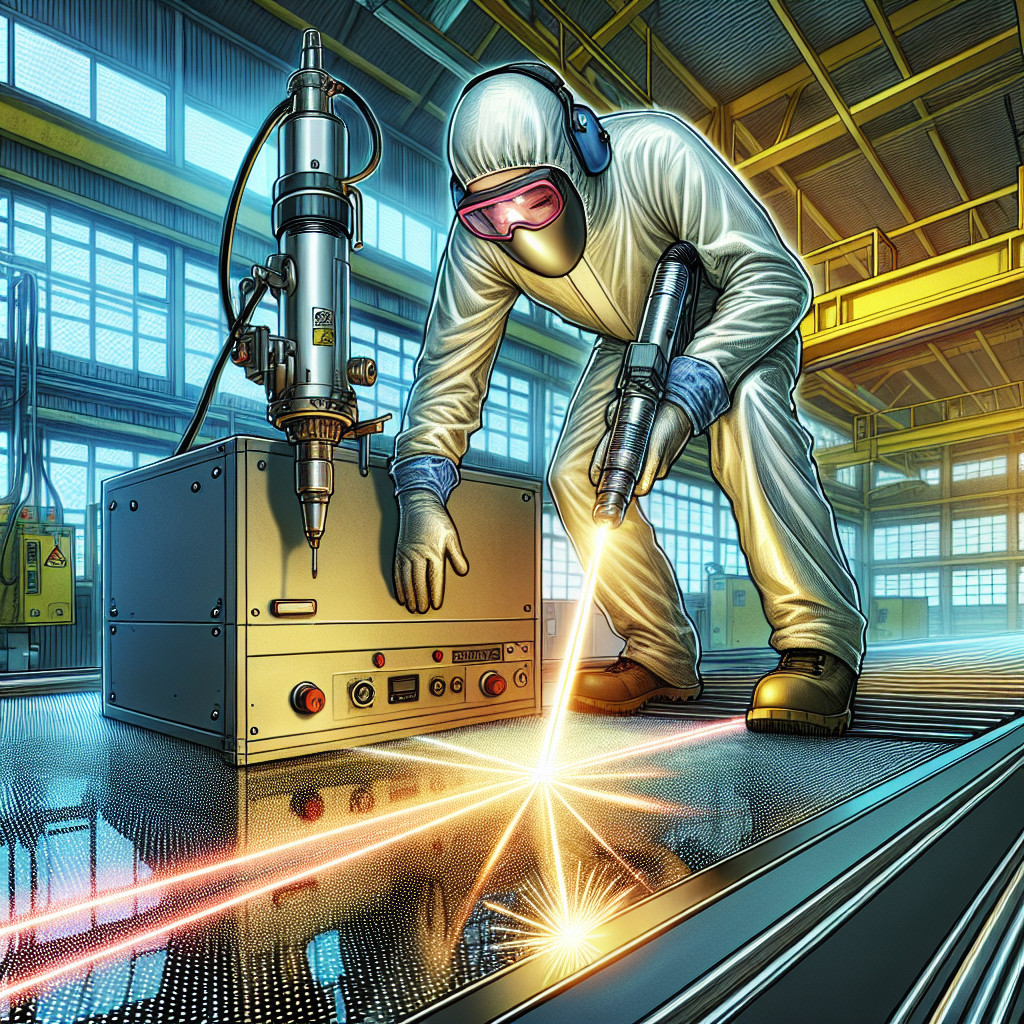
- Principles of laser cleaning for adhesive residue removal
- Comparison of laser cleaning with traditional cleaning methods for adhesive residues
- Applications of laser cleaning in various industries for adhesive residue removal
- Safety considerations and precautions in laser cleaning for adhesive residues
- Cost analysis of laser cleaning for adhesive residue removal
- Laser cleaning for removing adhesive residues from wood surfaces
- Types of lasers used for adhesive residue removal
- Laser cleaning for removing adhesive residues from medical devices
Principles of laser cleaning for adhesive residue removal
Adhesive residues can be a common problem in various industries, including manufacturing, automotive, electronics, and even in everyday household items. These residues can be stubborn and difficult to remove, often requiring time-consuming and labor-intensive methods. However, laser cleaning has emerged as an efficient and effective solution for adhesive residue removal. In this article, we will explore the principles of laser cleaning and how it can be applied to remove adhesive residues.
Understanding Laser Cleaning:
Laser cleaning is a non-contact, non-abrasive, and environmentally friendly method of surface cleaning. It utilizes the power of laser beams to remove contaminants, such as adhesive residues, without damaging the underlying surface. The process involves the interaction between the laser beam and the adhesive residue, resulting in the vaporization or sublimation of the residue, leaving behind a clean surface.
Principles of Laser Cleaning:
1. Absorption: Laser beams are absorbed by the adhesive residue, converting the light energy into heat energy. This heat causes the residue to reach its vaporization or sublimation temperature, leading to its removal.
2. Selective Absorption: Different materials have different absorption coefficients for laser beams. Laser cleaning takes advantage of this property by selecting a laser wavelength that is highly absorbed by the adhesive residue but minimally absorbed by the underlying surface. This ensures that only the residue is removed, leaving the surface intact.
3. Pulse Duration: The duration of the laser pulse plays a crucial role in the cleaning process. Shorter pulse durations result in higher peak powers, which can effectively remove adhesive residues. However, longer pulse durations can be used for delicate surfaces to avoid any damage.
4. Laser Intensity: The intensity of the laser beam determines the amount of energy delivered to the adhesive residue. By adjusting the laser intensity, the cleaning process can be optimized for different types and thicknesses of adhesive residues.
Advantages of Laser Cleaning for Adhesive Residue Removal:
1. Non-Destructive: Laser cleaning is a non-destructive method that does not damage the underlying surface. It removes only the adhesive residue, leaving the surface intact and undamaged.
2. Precision: Laser cleaning offers precise control over the cleaning process. The laser beam can be focused on specific areas, allowing for targeted removal of adhesive residues.
3. Efficiency: Laser cleaning is a highly efficient method that can remove adhesive residues quickly and effectively. It eliminates the need for manual scraping or the use of harsh chemicals, saving time and reducing labor costs.
4. Environmentally Friendly: Laser cleaning is an environmentally friendly method as it does not involve the use of chemicals or produce any harmful by-products. It is a clean and sustainable solution for adhesive residue removal.
Keywords: laser cleaning, adhesive residue removal, non-contact cleaning, non-abrasive cleaning, environmentally friendly cleaning, selective absorption, pulse duration, laser intensity, non-destructive cleaning, precision cleaning, efficient cleaning, environmentally friendly cleaning.
Long-tail Phrases:
1. .
2. Understanding the process of laser cleaning for adhesive residue removal.
3. Advantages of laser cleaning for efficient adhesive residue removal.
4. Selective absorption in laser cleaning for targeted adhesive residue removal.
5. The role of pulse duration and laser intensity in laser cleaning for adhesive residue removal.
6. Laser cleaning as a non-destructive and environmentally friendly method for adhesive residue removal.
Comparison of laser cleaning with traditional cleaning methods for adhesive residues
W dzisiejszych czasach kleje są szeroko stosowane w różnych branżach, takich jak przemysł samochodowy, elektronika, przemysł spożywczy i wiele innych. Jednak po zakończeniu procesu klejenia często pozostają niechciane resztki kleju na powierzchniach, które mogą być trudne do usunięcia. Istnieje wiele tradycyjnych metod czyszczenia, takich jak mechaniczne ścieranie, stosowanie rozpuszczalników chemicznych, a nawet zastosowanie wysokiego ciśnienia wody. Jednak w ostatnich latach coraz większą popularność zdobywa czyszczenie laserowe jako alternatywna metoda usuwania pozostałości kleju.
Czyszczenie laserowe jest procesem, w którym skoncentrowane wiązki laserowe są skierowane na powierzchnię, aby usunąć zanieczyszczenia. W przypadku pozostałości kleju, laser jest w stanie skierować energię na te obszary, co powoduje odparowanie lub odłuszczenie kleju. Istnieje wiele zalet czyszczenia laserowego w porównaniu do tradycyjnych metod czyszczenia.
Po pierwsze, czyszczenie laserowe jest nieinwazyjne i nie powoduje uszkodzeń powierzchni. Tradycyjne metody czyszczenia, takie jak mechaniczne ścieranie, mogą prowadzić do zarysowań lub uszkodzeń powierzchni, zwłaszcza w przypadku delikatnych materiałów. Czyszczenie laserowe jest precyzyjne i kontrolowane, co minimalizuje ryzyko uszkodzenia.
Po drugie, czyszczenie laserowe jest bardziej ekologiczne. Tradycyjne metody czyszczenia często wymagają stosowania chemicznych rozpuszczalników, które mogą być szkodliwe dla środowiska. Czyszczenie laserowe nie wymaga stosowania żadnych substancji chemicznych, co czyni go bardziej przyjaznym dla środowiska.
Po trzecie, czyszczenie laserowe jest bardziej efektywne i skuteczne. Laser jest w stanie skierować energię na konkretne obszary, co oznacza, że pozostałości kleju mogą być usuwane dokładnie i kompletnie. Tradycyjne metody czyszczenia mogą być czasochłonne i nie zawsze skuteczne w usuwaniu trudnych do usunięcia resztek kleju.
Jednak czyszczenie laserowe ma również pewne ograniczenia. Po pierwsze, jest to kosztowna metoda czyszczenia, ponieważ wymaga specjalistycznego sprzętu i wyszkolonego personelu. Tradycyjne metody czyszczenia mogą być tańsze i bardziej dostępne dla wielu przedsiębiorstw. Po drugie, czyszczenie laserowe może być ograniczone w przypadku niektórych materiałów, takich jak tworzywa sztuczne, które mogą reagować na działanie lasera.
Wnioskiem jest to, że czyszczenie laserowe jest obiecującą alternatywą dla tradycyjnych metod czyszczenia pozostałości kleju. Posiada wiele zalet, takich jak nieinwazyjność, ekologiczność i skuteczność. Jednak koszty i ograniczenia techniczne mogą stanowić wyzwanie dla niektórych przedsiębiorstw. W związku z tym, przed podjęciem decyzji o zastosowaniu czyszczenia laserowego, należy dokładnie zbadać i porównać różne metody czyszczenia, aby znaleźć najlepsze rozwiązanie dla konkretnych potrzeb.
Słowa kluczowe: czyszczenie laserowe, tradycyjne metody czyszczenia, pozostałości kleju, mechaniczne ścieranie, rozpuszczalniki chemiczne, wysokie ciśnienie wody, nieinwazyjne, ekologiczne, efektywne, kosztowne, ograniczenia techniczne.
Frazy kluczowe: porównanie czyszczenia laserowego z tradycyjnymi metodami czyszczenia dla pozostałości kleju, zalety i wady czyszczenia laserowego, skuteczność czyszczenia laserowego w usuwaniu pozostałości kleju, ekologiczność czyszczenia laserowego, koszty czyszczenia laserowego, ograniczenia techniczne czyszczenia laserowego.
Applications of laser cleaning in various industries for adhesive residue removal
In the automotive industry, adhesive residue removal is crucial during the manufacturing process, maintenance, and repair of vehicles. Laser cleaning can effectively remove adhesive residues from car bodies, windshields, headlights, and other components without damaging the underlying surfaces. This ensures proper adhesion of new components, improves the overall appearance of the vehicle, and reduces the risk of defects or failures.
Electronics Industry:
The electronics industry heavily relies on adhesives for bonding components and securing electronic devices. However, adhesive residue left behind during manufacturing or repair processes can interfere with the performance and reliability of electronic devices. Laser cleaning provides a precise and controlled method for removing adhesive residues from delicate electronic components, circuit boards, and connectors. This helps maintain the integrity of the electronic devices and ensures optimal functionality.
Aerospace Industry:
In the aerospace industry, adhesive residue removal is essential for maintaining the structural integrity and performance of aircraft components. Laser cleaning can effectively remove adhesive residues from composite materials, metal surfaces, and sensitive aerospace equipment. This ensures proper bonding of components, reduces the risk of corrosion, and improves the overall safety and efficiency of aircraft.
Medical Industry:
In the medical industry, adhesive residue removal is critical for maintaining the cleanliness and functionality of medical devices and equipment. Laser cleaning can safely and effectively remove adhesive residues from surgical instruments, medical implants, and other medical equipment without causing damage or contamination. This helps prevent infections, ensures accurate readings, and prolongs the lifespan of medical devices.
Renewable Energy Industry:
The renewable energy industry, including solar and wind power, relies on adhesives for securing panels, blades, and other components. Over time, adhesive residues can accumulate on these surfaces, reducing the efficiency of renewable energy systems. Laser cleaning offers a non-destructive method for removing adhesive residues from solar panels, wind turbine blades, and other renewable energy equipment. This improves the performance and longevity of these systems, ultimately contributing to a more sustainable future.
Keywords: laser cleaning, adhesive residue removal, various industries, automotive industry, electronics industry, aerospace industry, medical industry, renewable energy industry.
Long-tail phrases:
1. Laser cleaning for adhesive residue removal in the automotive industry.
2. Applications of laser cleaning in the electronics industry for adhesive residue removal.
3. Laser cleaning in the aerospace industry: removing adhesive residues for improved performance.
4. The role of laser cleaning in the medical industry for adhesive residue removal.
5. Laser cleaning for adhesive residue removal in the renewable energy industry: a sustainable solution.
Safety considerations and precautions in laser cleaning for adhesive residues
Laser cleaning involves the use of high-powered lasers, which can pose potential hazards if not handled properly. It is essential to follow laser safety guidelines to prevent accidents and injuries. Operators should wear appropriate laser safety goggles that provide adequate protection against the specific wavelength of the laser being used. Additionally, the laser cleaning system should be equipped with safety features such as interlocks and emergency stop buttons to ensure immediate shutdown in case of any unforeseen circumstances.
2. Ventilation:
During laser cleaning, the process can generate fumes and vapors, especially when removing adhesive residues. Adequate ventilation should be provided in the cleaning area to prevent the accumulation of potentially harmful substances. This can be achieved by using local exhaust ventilation systems or ensuring that the cleaning area is well-ventilated with fresh air circulation. Proper ventilation helps in maintaining a safe working environment and reduces the risk of inhalation of hazardous substances.
3. Personal Protective Equipment (PPE):
In addition to laser safety goggles, operators should wear appropriate personal protective equipment (PPE) to minimize the risk of injuries. This may include gloves, lab coats, and closed-toe shoes to protect against potential burns, cuts, or chemical exposure. The type of PPE required may vary depending on the specific adhesive residues being cleaned and the cleaning environment. It is essential to assess the potential hazards and provide the necessary protective gear accordingly.
4. Training and Certification:
Operators should undergo comprehensive training on laser safety and the proper use of laser cleaning equipment. They should be familiar with the specific hazards associated with adhesive residues and understand the safety precautions required to mitigate those risks. Certification programs can ensure that operators have the necessary knowledge and skills to perform laser cleaning safely. Regular refresher courses and updates on safety protocols should be provided to keep operators informed about the latest developments in laser cleaning technology and safety practices.
5. Surface Compatibility:
Before using laser cleaning for adhesive residues, it is crucial to assess the compatibility of the surface being cleaned with the laser. Different materials may react differently to laser cleaning, and some surfaces may be more susceptible to damage or discoloration. Conducting a small test patch on an inconspicuous area can help determine the suitability of laser cleaning for a particular surface. It is also essential to consider the thickness and condition of the adhesive residues to ensure that laser cleaning is the most appropriate method for removal.
6. Environmental Considerations:
Laser cleaning is considered an environmentally friendly cleaning method as it does not involve the use of chemicals or produce harmful by-products. However, it is still important to consider the environmental impact of laser cleaning for adhesive residues. Proper disposal of removed residues should be carried out in accordance with local regulations. Additionally, the energy consumption of the laser cleaning system should be optimized to minimize its carbon footprint.
Keywords: laser cleaning, adhesive residues, safety considerations, precautions, laser safety, ventilation, personal protective equipment, training, certification, surface compatibility, environmental considerations.
Long-tail phrases:
– Safety measures and precautions in laser cleaning for adhesive residues
– Laser cleaning for adhesive residues: safety considerations and precautions
– Importance of safety in laser cleaning for adhesive residues
– Laser cleaning for adhesive residues: surface compatibility and safety precautions
– Environmental considerations in laser cleaning for adhesive residues.
Cost analysis of laser cleaning for adhesive residue removal
The initial investment in laser cleaning equipment is a significant consideration. Laser cleaning systems range in price depending on their power, capabilities, and brand. Higher-powered lasers with advanced features may have a higher upfront cost but can offer faster and more efficient cleaning. It is essential to evaluate the specific requirements of the application and choose a laser system that provides the necessary power and functionality while considering the long-term cost-effectiveness.
Operational Expenses:
While the equipment cost is a one-time investment, operational expenses play a crucial role in the overall cost analysis. Laser cleaning requires a power source, which contributes to electricity costs. However, compared to other cleaning methods, laser cleaning is generally more energy-efficient, resulting in lower electricity consumption. Additionally, laser cleaning eliminates the need for consumables such as solvents, brushes, or abrasive materials, reducing ongoing material costs. The maintenance and servicing of the laser system should also be considered as part of the operational expenses.
Labor Costs:
Labor costs are a significant component of any cleaning process. Traditional methods often require manual labor for scraping or applying solvents, which can be time-consuming and labor-intensive. Laser cleaning, on the other hand, is a relatively automated process, reducing the need for extensive manual labor. This can result in significant labor cost savings, especially for large-scale operations or repetitive cleaning tasks. However, it is important to consider the training and expertise required to operate the laser cleaning equipment effectively.
Cleaning Efficiency and Time Savings:
The efficiency of adhesive residue removal is a crucial factor in the cost analysis. Laser cleaning offers precise and targeted cleaning, ensuring complete removal of adhesive residues without damaging the underlying surface. This eliminates the need for rework or additional cleaning steps, saving both time and resources. The speed of laser cleaning is also noteworthy, as it can clean large areas quickly, further reducing the overall cleaning time and increasing productivity.
Environmental Impact:
In addition to cost considerations, the environmental impact of the cleaning method should be evaluated. Traditional methods often involve the use of chemical solvents, which can be harmful to the environment and require proper disposal. Laser cleaning, on the other hand, is a non-contact and chemical-free process, making it environmentally friendly. This can lead to potential cost savings in terms of waste management and compliance with environmental regulations.
Conclusion:
In conclusion, laser cleaning offers a cost-effective solution for adhesive residue removal. While the initial investment in equipment may be higher, the operational expenses, labor cost savings, and increased efficiency outweigh the upfront cost. Laser cleaning eliminates the need for consumables, reduces cleaning time, and minimizes the environmental impact. The key to maximizing the cost-effectiveness of laser cleaning lies in selecting the appropriate equipment, considering the specific requirements of the application. Overall, laser cleaning proves to be a valuable and efficient method for adhesive residue removal in various industries.
Keywords: laser cleaning, adhesive residue removal, cost analysis, equipment cost, operational expenses, labor costs, cleaning efficiency, time savings, environmental impact.
Long-tail phrases:
1. Cost-effective adhesive residue removal using laser cleaning.
2. Laser cleaning as an efficient alternative for adhesive residue removal.
3. Evaluating the cost-effectiveness of laser cleaning for adhesive residue removal.
4. The impact of laser cleaning on labor costs and cleaning efficiency.
5. Environmental benefits of laser cleaning for adhesive residue removal.
Laser cleaning for removing adhesive residues from wood surfaces
Laser cleaning is a non-contact, non-abrasive, and environmentally friendly method of removing contaminants from various surfaces. It involves the use of a high-intensity laser beam that selectively heats and vaporizes the adhesive residues, leaving the underlying wood surface intact. The laser beam’s energy is absorbed by the adhesive, causing it to break down and evaporate, resulting in a clean and residue-free surface.
Advantages of Laser Cleaning for Removing Adhesive Residues:
1. Non-destructive: Laser cleaning does not damage the wood surface, ensuring the integrity and aesthetics of the material.
2. Precision: The laser beam can be precisely controlled, allowing for targeted cleaning of specific areas without affecting the surrounding wood.
3. Versatility: Laser cleaning can be used on various types of wood surfaces, including hardwood, softwood, veneers, and laminates.
4. Efficiency: Laser cleaning is a fast and efficient method, reducing the time and effort required for adhesive residue removal.
5. Environmentally friendly: Unlike traditional cleaning methods that involve the use of chemicals, laser cleaning is a clean and green process that does not produce any harmful by-products.
Laser Cleaning Process for Removing Adhesive Residues:
1. Surface Preparation: Before laser cleaning, the wood surface should be prepared by removing any loose debris or particles. This ensures optimal contact between the laser beam and the adhesive residues.
2. Laser Parameters: The laser parameters, including power, pulse duration, and spot size, are adjusted based on the type and thickness of the adhesive residues and the wood surface. These parameters determine the energy delivered to the adhesive, ensuring effective removal without damaging the wood.
3. Laser Cleaning: The laser beam is directed onto the adhesive residues, causing them to heat up and vaporize. The laser operator carefully controls the movement of the laser beam to ensure complete coverage of the affected area.
4. Post-Cleaning Inspection: After laser cleaning, the wood surface is inspected to ensure that all adhesive residues have been successfully removed. Any remaining residues can be targeted with additional laser cleaning or alternative cleaning methods if necessary.
Keywords: laser cleaning, adhesive residues, wood surfaces, non-destructive, precision, efficiency, environmentally friendly.
Long-tail phrases:
1. Laser cleaning as a non-destructive method for removing adhesive residues from wood surfaces.
2. The advantages of laser cleaning over traditional cleaning methods for adhesive residue removal on wood surfaces.
3. The process of laser cleaning for effectively removing adhesive residues from wood surfaces.
4. The environmental benefits of laser cleaning for adhesive residue removal on wood surfaces.
5. The versatility of laser cleaning for different types of wood surfaces and adhesive residues.
Types of lasers used for adhesive residue removal
1. CO2 lasers:
CO2 lasers are one of the most commonly used types of lasers for adhesive residue removal. These lasers emit a high-intensity beam of infrared light, which is absorbed by the adhesive residue, causing it to heat up and vaporize. CO2 lasers are highly effective in removing a wide range of adhesive residues, including those from tapes, labels, and stickers. They are also suitable for use on various surfaces, including metals, plastics, and glass.
2. Nd:YAG lasers:
Nd:YAG lasers, or neodymium-doped yttrium aluminum garnet lasers, are another popular choice for adhesive residue removal. These lasers emit a high-energy beam of light in the near-infrared spectrum. Nd:YAG lasers are particularly effective in removing adhesive residues from metals, ceramics, and other heat-resistant materials. They can also be used for precision cleaning of delicate surfaces, such as electronic components.
3. Fiber lasers:
Fiber lasers are a newer addition to the field of adhesive residue removal. These lasers use optical fibers to deliver the laser beam, resulting in a compact and flexible design. Fiber lasers offer high power and excellent beam quality, making them suitable for removing adhesive residues from a variety of surfaces, including metals, plastics, and composites. They are also known for their energy efficiency and low maintenance requirements.
4. Excimer lasers:
Excimer lasers are a type of ultraviolet laser commonly used in industrial applications. These lasers emit short pulses of high-energy ultraviolet light, which can break down and remove adhesive residues effectively. Excimer lasers are particularly useful for removing residues from sensitive surfaces, such as semiconductors and optical components. They are also capable of removing residues without causing damage or leaving any trace behind.
In conclusion, lasers have emerged as a powerful tool for adhesive residue removal. CO2 lasers, Nd:YAG lasers, fiber lasers, and excimer lasers are some of the commonly used types of lasers for this purpose. Each type offers unique advantages and applications, allowing for efficient and precise removal of adhesive residues from various surfaces. Laser-based methods not only save time and effort but also ensure a clean and residue-free surface. As industries continue to evolve, laser technology will likely play an increasingly important role in adhesive residue removal.
Keywords: adhesive residue removal, lasers, CO2 lasers, Nd:YAG lasers, fiber lasers, excimer lasers, precision cleaning, surface cleaning, industrial applications, non-contact cleaning.
Long-tail phrases:
– Laser-based methods for adhesive residue removal
– Advantages of using lasers for adhesive residue removal
– Applications of CO2 lasers in adhesive residue removal
– Nd:YAG lasers for precision cleaning of delicate surfaces
– Fiber lasers for efficient removal of adhesive residues
– Excimer lasers for residue-free cleaning of sensitive surfaces.
Laser cleaning for removing adhesive residues from medical devices
There are several advantages to using . Firstly, it is a highly precise method that can target specific areas without damaging the surrounding materials. This is particularly important when dealing with delicate medical devices that require careful handling. Laser cleaning can remove adhesive residues from intricate and hard-to-reach areas, ensuring a thorough cleaning process.
Secondly, laser cleaning is a fast and efficient method. It can remove adhesive residues in a matter of seconds, significantly reducing the cleaning time compared to traditional methods such as manual scraping or chemical solvents. This not only improves productivity but also reduces the risk of human error and contamination.
Furthermore, laser cleaning is a safe and environmentally friendly method. It does not involve the use of harsh chemicals or solvents that can be harmful to both the operator and the environment. Laser cleaning also produces minimal waste, as the vaporized residues can be easily collected and disposed of properly.
In addition to its effectiveness in removing adhesive residues, laser cleaning can also provide other benefits for medical devices. The laser energy can sterilize the surface, eliminating any potential pathogens or bacteria that may be present. This can help maintain the cleanliness and sterility of the medical devices, reducing the risk of infections or complications during their use.
Moreover, laser cleaning can improve the overall aesthetics of medical devices. Adhesive residues can leave unsightly marks or discoloration on the surface, affecting the visual appeal of the device. Laser cleaning can restore the original appearance of the device, enhancing its marketability and customer satisfaction.
In conclusion, laser cleaning is a highly effective and efficient method for removing adhesive residues from medical devices. Its precision, speed, safety, and environmental friendliness make it an ideal choice for manufacturers and healthcare professionals. By utilizing laser cleaning, medical devices can be thoroughly cleaned, sterilized, and restored to their original condition. This ensures their functionality, safety, and visual appeal, ultimately benefiting both the manufacturers and end-users.
Keywords: laser cleaning, adhesive residues, medical devices, non-contact, non-abrasive, environmentally friendly, precise, fast, efficient, safe, sterilization, aesthetics.
Long-tail phrases:
– : an effective and efficient method.
– The advantages of laser cleaning in the medical device industry.
– How laser cleaning improves the functionality and safety of medical devices.
– The environmental benefits of laser cleaning for adhesive residue removal.
– Laser cleaning: a non-contact and non-abrasive solution for adhesive residue removal.
– The role of laser cleaning in maintaining the cleanliness and sterility of medical devices.
– Enhancing the visual appeal of medical devices through laser cleaning.
– Laser cleaning: a time-saving solution for adhesive residue removal in the medical device industry.
– The precision and safety of laser cleaning for delicate medical devices.
– Laser cleaning: a sustainable approach to adhesive residue removal in the medical device industry.
- WebMakers Talks – business side of Sylius - 24 April 2024
- Laser cleaning for removing adhesive residues - 31 January 2024
- The most popular mobile application programming languages - 31 January 2024